How to make a block making machine?
There are various types of concrete blocks on the building materials market, including cinder blocks. They are characterized by low weight, increased size, which allows you to build a building at an accelerated pace. Wanting to reduce the estimated cost of work, many developers do not purchase block building materials, but make it on their own using a block production machine. Not always industrial models of vibration machines differ in quality and performance. It is easy to make a homemade unit, guided by the recommendations given.
Cinder blocks
Types of concrete blocks for construction
Despite the fact that brick is often used in the construction industry for the construction of buildings, it is difficult for it to compete with block building materials made of concrete. To build a house, it is easy to pick up blocks that differ:
- increased dimensions;
- reduced weight;
- filler used;
- production technology.
The manufacturing technology of block products provides for the use of the following filler:
- expanded clay;
- sawdust;
- slag;
- brick fight;
- dropouts.
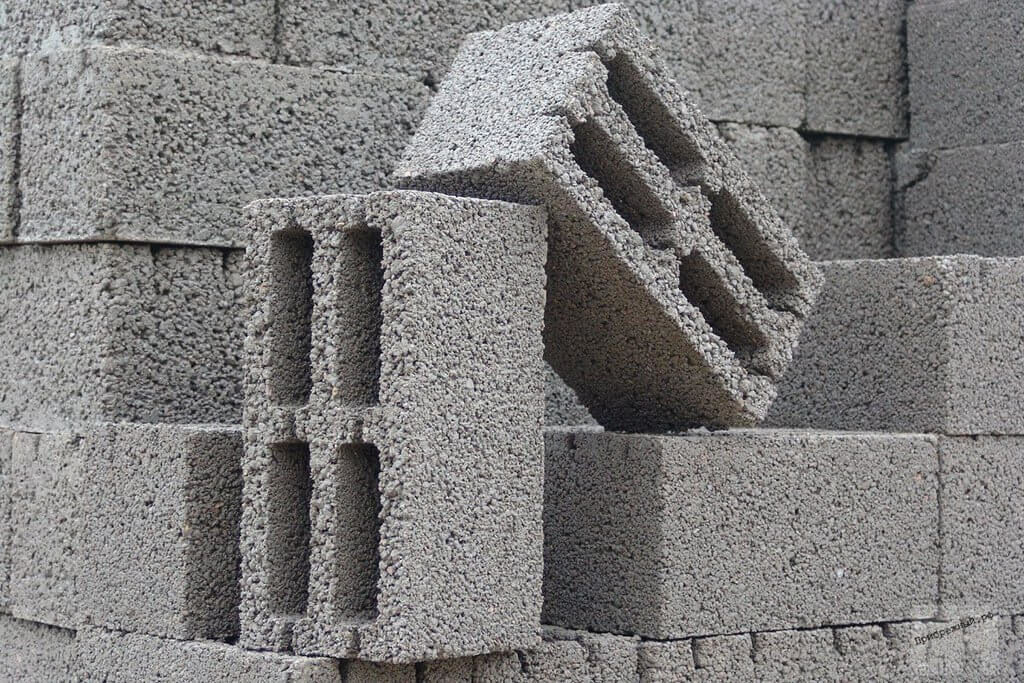
Block-type wall materials are divided into the following types:
- expanded clay concrete blocks;
- arbolite products;
- foam concrete building materials;
- aerated concrete products;
- cinder blocks.
The use of cinder blocks, the cost of which is lower than other block building materials, reduces the cost of building a building. Making cinder blocks on your own is easy to do at home using a block production machine. Consider the characteristics of cinder block building materials.
Cinder blocks - building material properties
Cinder blocks are a building material obtained by vibratory pressing technology. Along with cement and sand, the following types of filler are used for manufacturing:
- slag, which is a waste of metallurgical enterprises;
- screenings from granite and gravel;
- brick waste;
- river gravel;
- expanded clay particles.
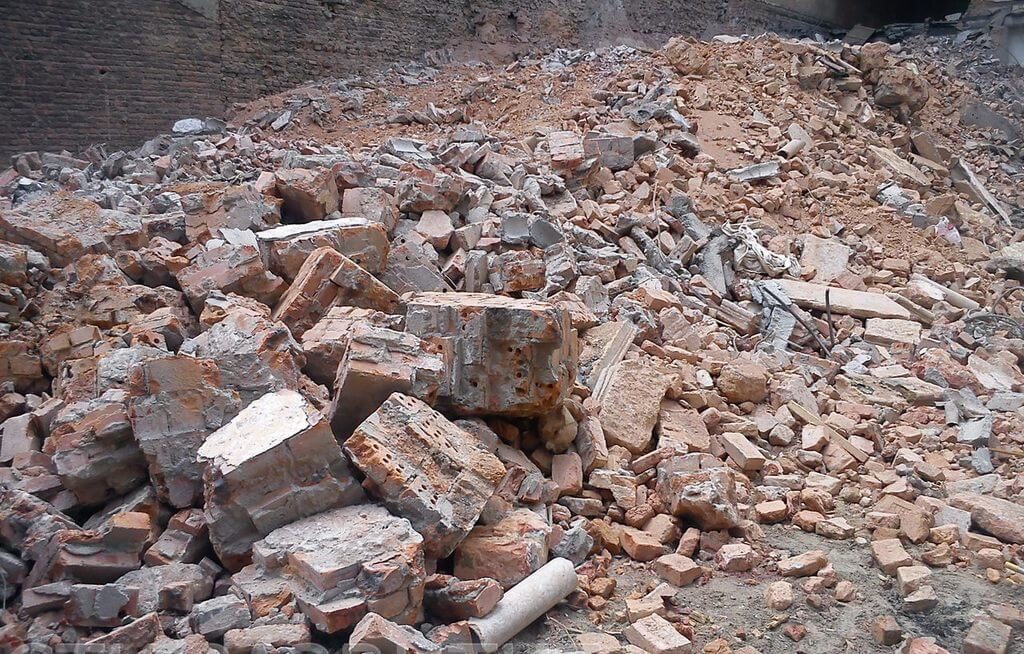
The manufacture of cinder block products can be carried out in various ways:
- according to industrial technology, providing for heat treatment and steaming;
- at home using a homemade block machine.
By making cinder blocks on the block machine, you can get products with the following advantages:
- improved thermal insulation properties. Slag concrete has low thermal conductivity and retains heat well;
- increased dimensions. They allow you to quickly build a cinder-block building, an outbuilding or a garage with your own hands;
- resistance to microorganisms and damage by rodents. This is ensured by the filler used and the structure of the cinder block array;
- reduced cost. A home-made cinder block is cheaper than, for example, a foam block purchased in a distribution network used for construction.
In addition, cinder-concrete material is fireproof, easy to process and dampens external noise.
Along with the advantages, slag concrete has a number of disadvantages:
- limited service life. The durability of the cinder concrete structure does not exceed two and a half decades;
- reduced strength properties. Only one-story and two-story buildings are erected from slag concrete;
- cracks when sheared. In the process of shrinking the box, cracks do not go along the seams, but directly along the blocks.
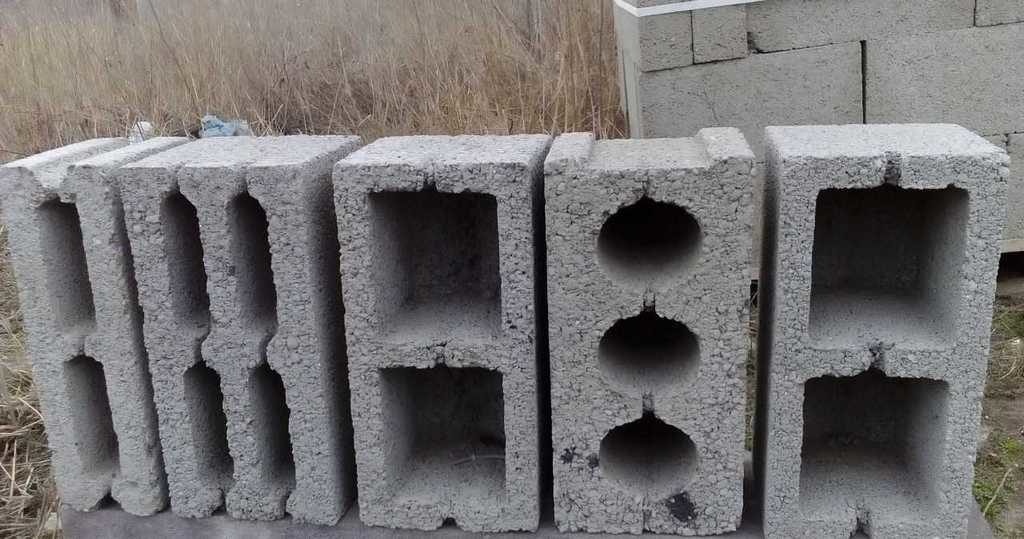
Slag concrete also has an unpresentable appearance and needs external finishing. In addition, slag concrete cannot be used for foundation construction.
Despite the weaknesses of the material, it is preferred in situations where it is required to quickly build a small building or outbuilding at minimal cost.
Which is better to use a block machine
Before developers who decide to independently produce cinder blocks for building walls, the question arises of choosing equipment. It is not always possible to rent a machine for the production of building blocks, especially in small towns. Many decide to make equipment on their own. Depending on financial capabilities, you can stop at the following options:
- the simplest design that allows you to make wall blocks at home at minimal cost;
- a modernized version of the unit, equipped with a sealing device and additional mechanisms.
It is difficult to give an unambiguous answer which machine for the production of blocks is preferable to use. It all depends on the number of blocks to be produced and funding opportunities. Let's take a look at the features of each unit.
Simplified Block Machine
For the manufacture of cinder blocks on your own in a reduced quantity, it is not necessary to manufacture a mechanized unit, use a vibrator, as well as additional mechanisms. The manufacturing process using simplified technology can be carried out in special forms.
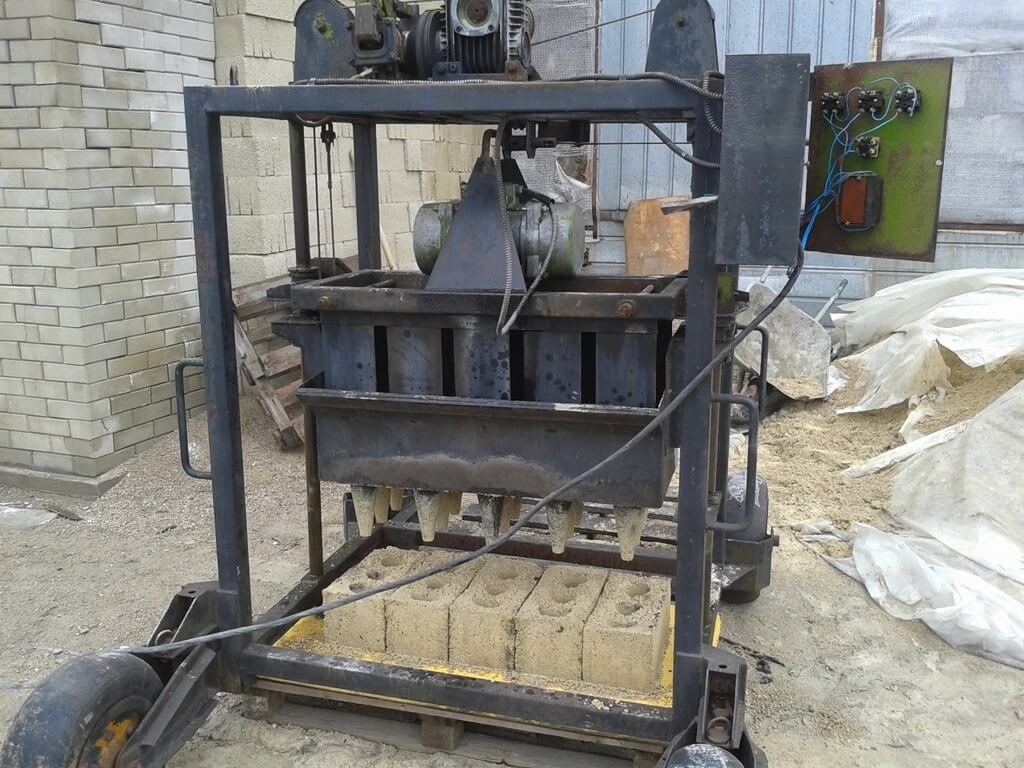
Procedure:
- Assemble the molds and coat their inner surface with used oil.
- Pour the cinder block mixture into collapsible forms.
- Leave for 3-4 hours until the solution hardens.
- Disassemble the containers and carefully remove the blocks.
- Allow to dry indoors.
If it is necessary to manufacture hollow products, it is advisable to use ordinary beverage bottles to form cavities. A simplified block machine, which is a container of the required size made of wood or steel, can be made at a minimum amount of effort.
Upgraded building block machine
With an increased need for cinder blocks for the construction of a large building, a more complex block production machine can be made, equipped with special devices:
- vibration mechanism. An electric motor is used as a vibration motor, on the drive shaft of which an eccentric is located. The drive power depends on the size of the form, the mass of the slag concrete solution and is 0.5–1.5 kW. Under the influence of vibration, the cinder concrete mass is compacted, the material is evenly distributed throughout the mold space, and air inclusions are removed. As a result of compaction, the specific gravity and strength of cinder block products increase;
- lifting device. It is designed for accelerated extraction of finished products from molding containers. There are many design solutions to speed up and facilitate the excavation of blocks. In the simplest version, it is enough to weld handles of arbitrary shape to the molding container, by pulling which you can remove the hardened block. Using ready-made drawings, you can independently assemble the lever mechanism from improvised materials.
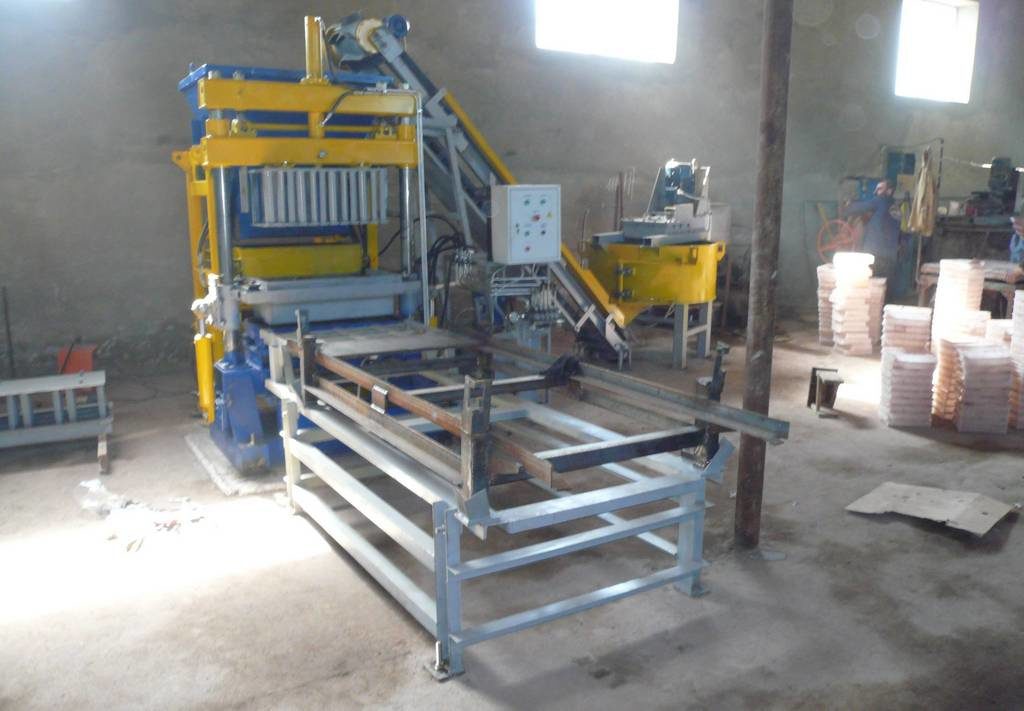
The form used in this unit must correspond to the dimensions of the cinder block that is planned to be made. In most cases, products of standard dimensions are manufactured - 0.4x0.2x0.2 m. The molding container must have a height increased by 4 m5 cm so that the molded block after compaction has the required dimensions. To simulate cavities, cut pipes of the required diameter can be welded to the bottom of the tank.
We make a machine for blocks with our own hands - a sequence of actions
To perform the assembly of the vibrocompactor, it is necessary to prepare. You will need the following materials and tools:
- steel sheets 2.5–3 mm thick;
- metal pipe with an outer diameter of 7.5m8.5 cm;
- electric motor with a power of up to one kilowatt;
- apparatus for electric welding with electrodes;
- grinder complete with a cutting wheel for metal;
- locksmith tool.
Before starting production, you should prepare drawings and deal with the design of the machine for the production of blocks. It is necessary to determine the dimensions of the blocks that will be manufactured - the size of the mold depends on this. It can be welded for standard products or made in an enlarged size.
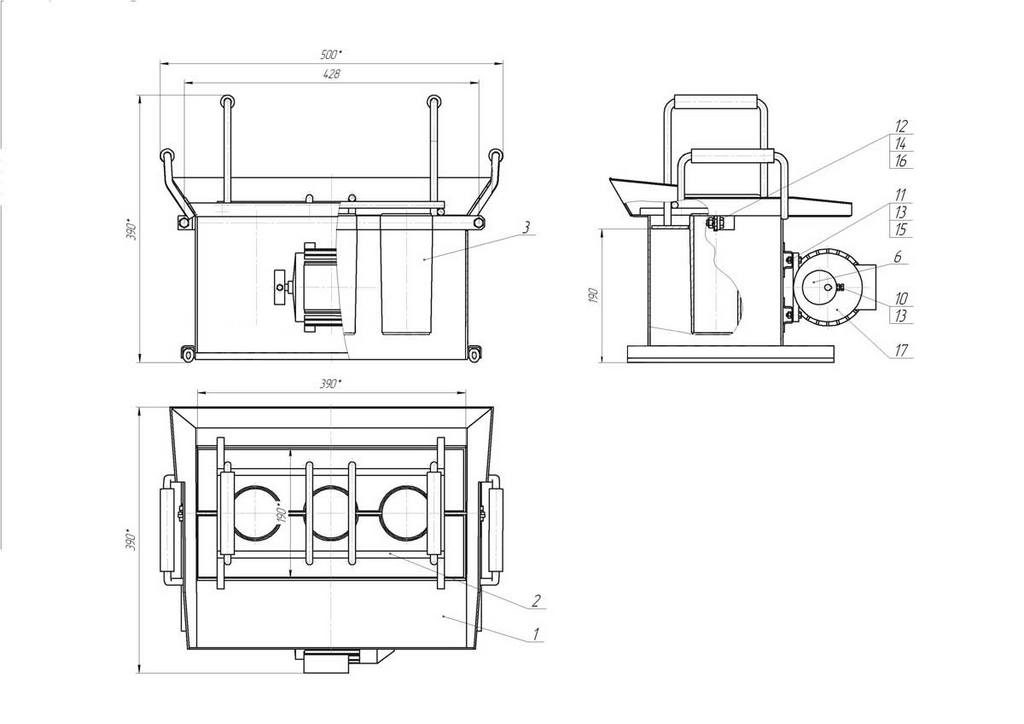
When everything is prepared, we make a machine for the production of block products, observing the sequence of operations:
- Cut a steel sheet into a rectangular shape to weld a molding container of the required size.
- Grab them with electric welding and assemble the side edging of the molding box for pouring the cinder block mixture.
- Check the correctness of the tack, with an equal length of the diagonal, finally weld the mold elements.
- Cut tubular blanks, the length of which is equal to the height of the form and make diametrical cuts on the side surface.
- Provide a cone-shaped tubular elements and weld them to the bottom sheet of the future mold box.
- Weld the transverse jumper to the cones, install the plugs on the ends with a smaller size.
- Make the final assembly of the forming box by welding the bottom with inserts to the edging.
- Fasten two handles on opposite sides for lifting and transporting the forming container.
- Install the vibration motor screw fasteners and screw the vibration motor with balance weight.
- Cut out the top cover to match the dimensions of the inside of the box and have holes for pipes.
- Apply an anti-corrosion coating, assemble the unit and check its operation.
The use of an oversized group tank allows you to increase the productivity of the vibrocompression machine.
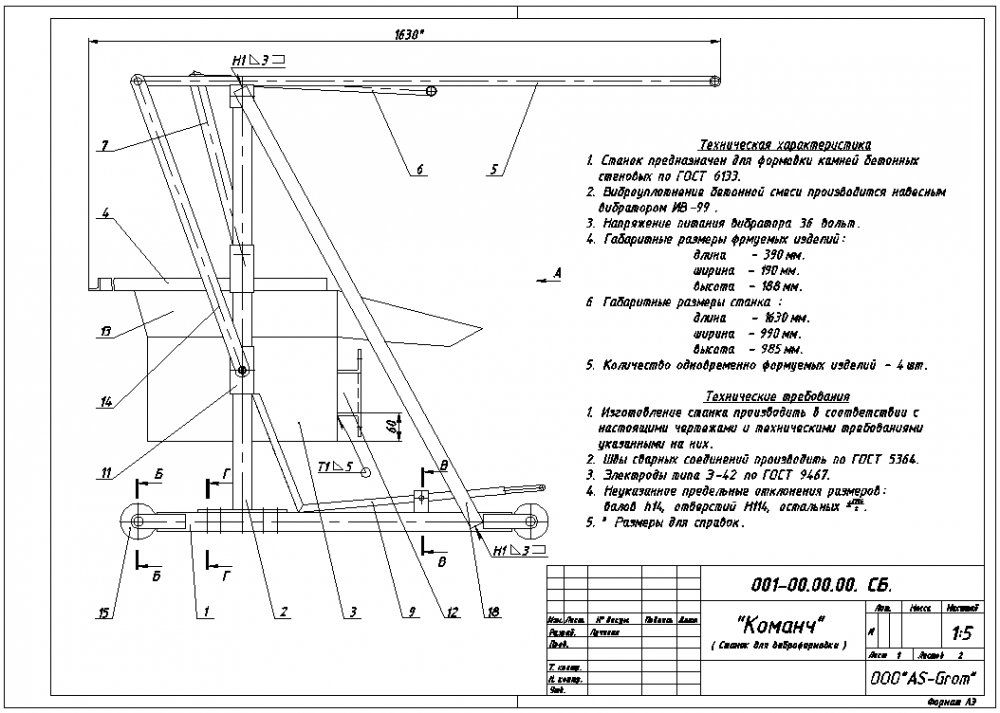
Independent production of cinder blocks - recipe
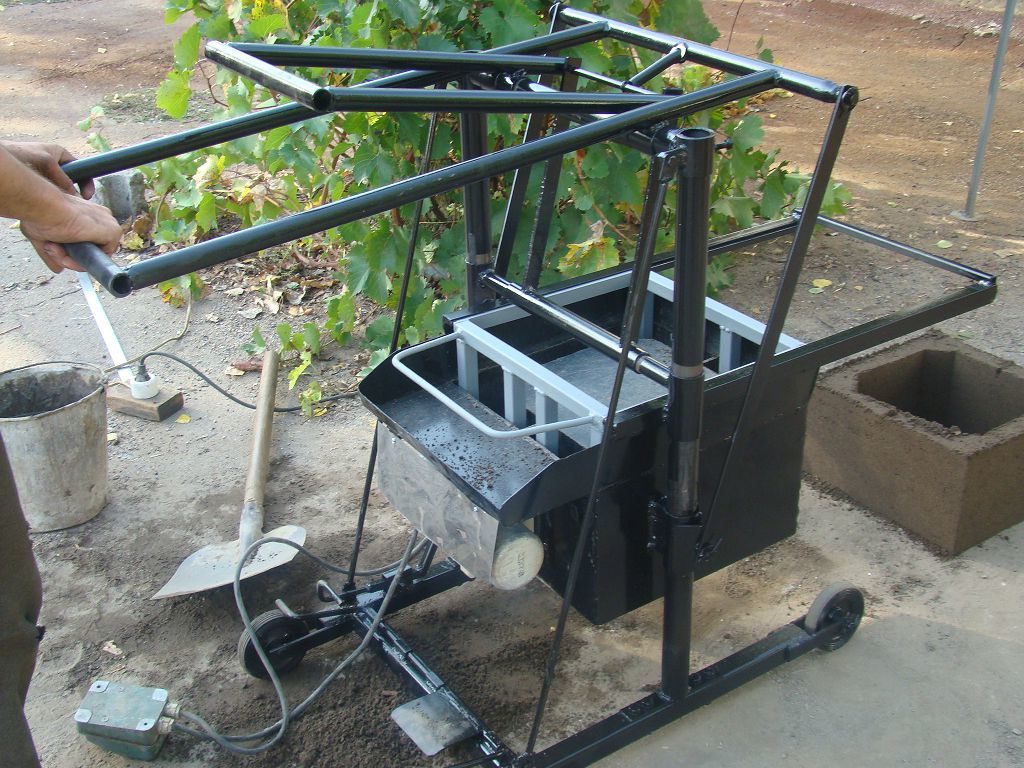
For the manufacture of cinder blocks on self-made equipment, it is necessary to prepare the following materials:
- Portland cement marked M400 and above;
- screenings or small gravel;
- slag or ash from coal combustion;
- sifted sand;
- water.
Special plasticizers are also used, which increase the strength of the cinder block mass and accelerate hardening. To prepare an increased volume of slag concrete mixture, a concrete mixer is required.
The following formulations of slag concrete composition are used:
- mix Portland cement with slag in a ratio of 1.5:8. Gradually dilute the mixture with water, the amount of which should not exceed half the volume of cement;
- mix crushed stone, cement and coal ash in a ratio of 4:1:4. Add water to the concrete mixer until the mortar is plastic.
Recipes are possible that involve the use of granulated slags, plasticizers, quartz sand and brick slaughter.
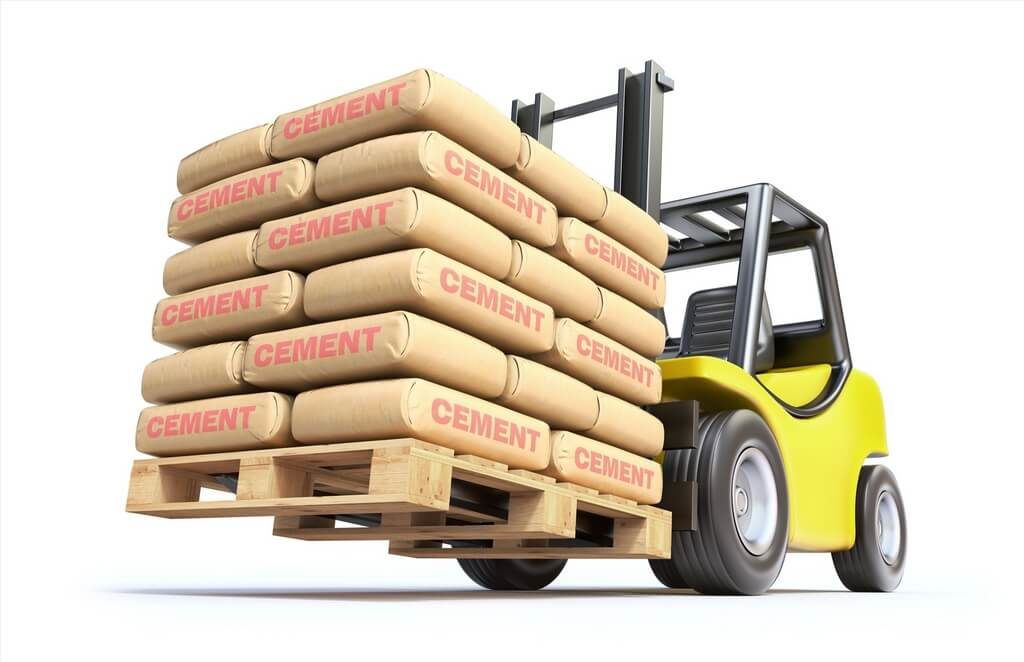
We manufacture products on our own, using a machine for the production of blocks
Using a self-made machine for blocks, carry out work according to the following algorithm:
- Install the equipment on level ground.
- Connect the electrical supply.
- Prepare a cinder block solution.
- Pour the prepared mixture into the mold.
- Turn on the vibration motor for 2-3 minutes.
- Add cinder block mixture to the top level.
- Replace the protective cover and turn on the vibrator.
Compact the array. The lid should come into contact with the stops located according to the height of the block. Then remove the box and let the molded block stand until the array sets. After careful removal, dry the cinder-concrete products in a closed and ventilated area.
Summing up
When planning the construction of a cinder block building, you can reduce the amount of costs by making a machine for the production of blocks yourself. It is important to use proven documentation for the manufacture of the unit and carefully understand the design of the vibration compactor. To obtain quality products, study the recipe, as well as understand the technology.